From automotive assembly lines to smart warehouses, AGV in manufacturing are redefining how we produce goods. In this article, Phenikaa-X will, alongside with you, dive deep into how AGVs in manufacturing transform production lines, their applications, benefits, challenges, and what the future holds for this technology.
1. What Are The AGV?
An AGV – Automated Guided Vehicle is a type of robotic vehicle designed to move materials autonomously within a factory. Using advanced guided-technologies like SLAM, Lidar sensor and cameras system, FMS,… these vehicles follow pre-programmed paths or adapt dynamically to their environment. With those technologies, AGV in manufacturing can operate without constant human oversight, making them a cornerstone of modern automation.
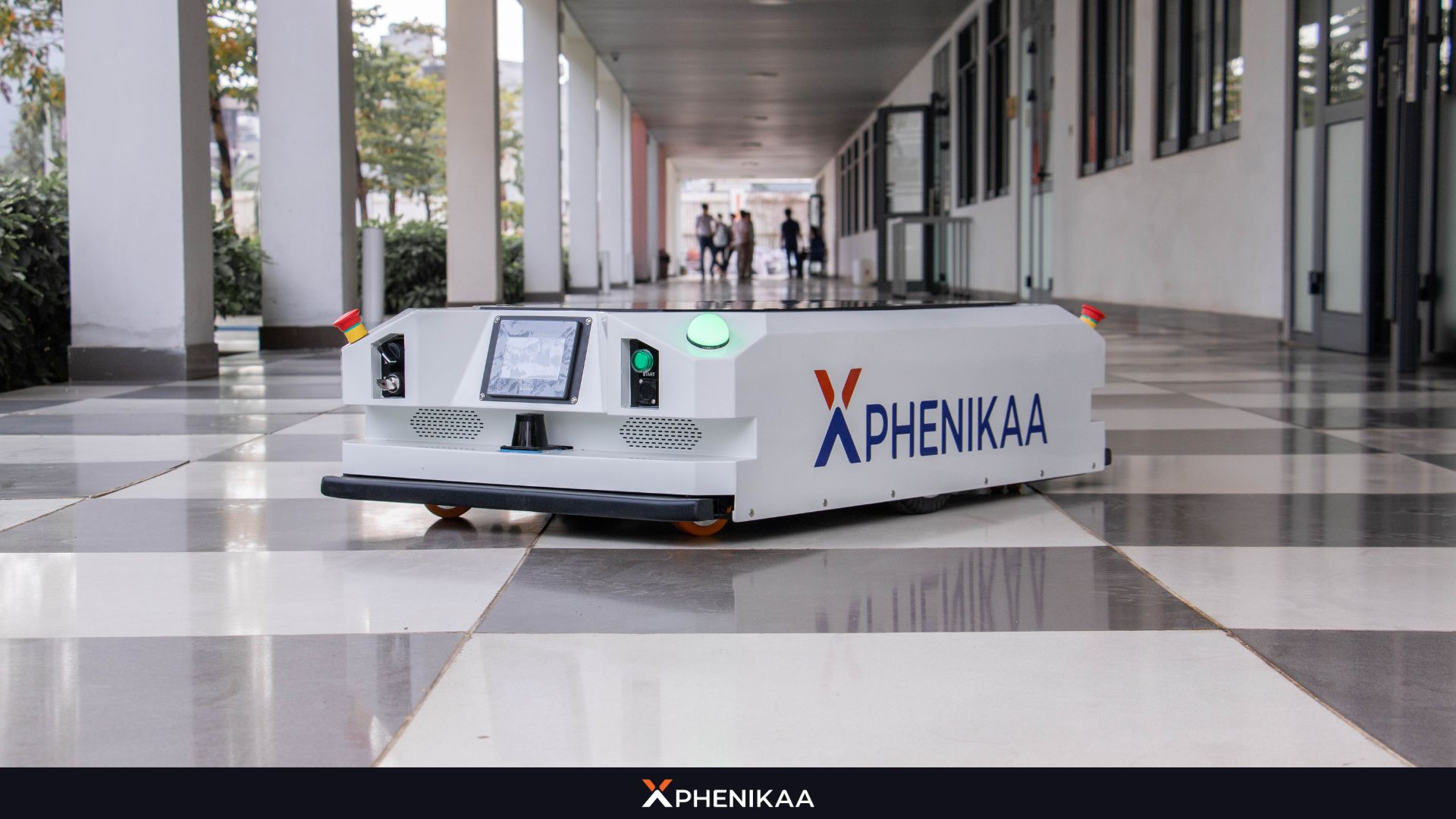
AGVs come in various types to suit different needs. Here are some of the most common types of AGV are currently being used widely around the world:
- Forklift AGVs: Lift and transport heavy pallets.
- Unit Load AGVs: Carry single loads like boxes or trays.
- Towing AGVs: Pull multiple carts for bulk transport.
- Assembly Line AGVs: Deliver parts directly to workstations.
Today, AGV technology takes a vital part for streamlining operations and boosting productivity in factories worldwide. As technology advances day by day, we will see more of this tech slowly appear more in our daily lives.
2. How AGVs Work in Manufacturing Environments
So, how does an AGV in manufacturing function? At its core, it relies on three key components: navigation, sensors and software:
- Navigation systems-such as LIDAR, GPS, or magnetic tape-guide the AGV along its route.
- Sensors detect obstacles, monitor loads, and ensure safe operation. Meanwhile.
- Fleet management software coordinates multiple manufacturing AGVs, optimizing their paths and schedules.
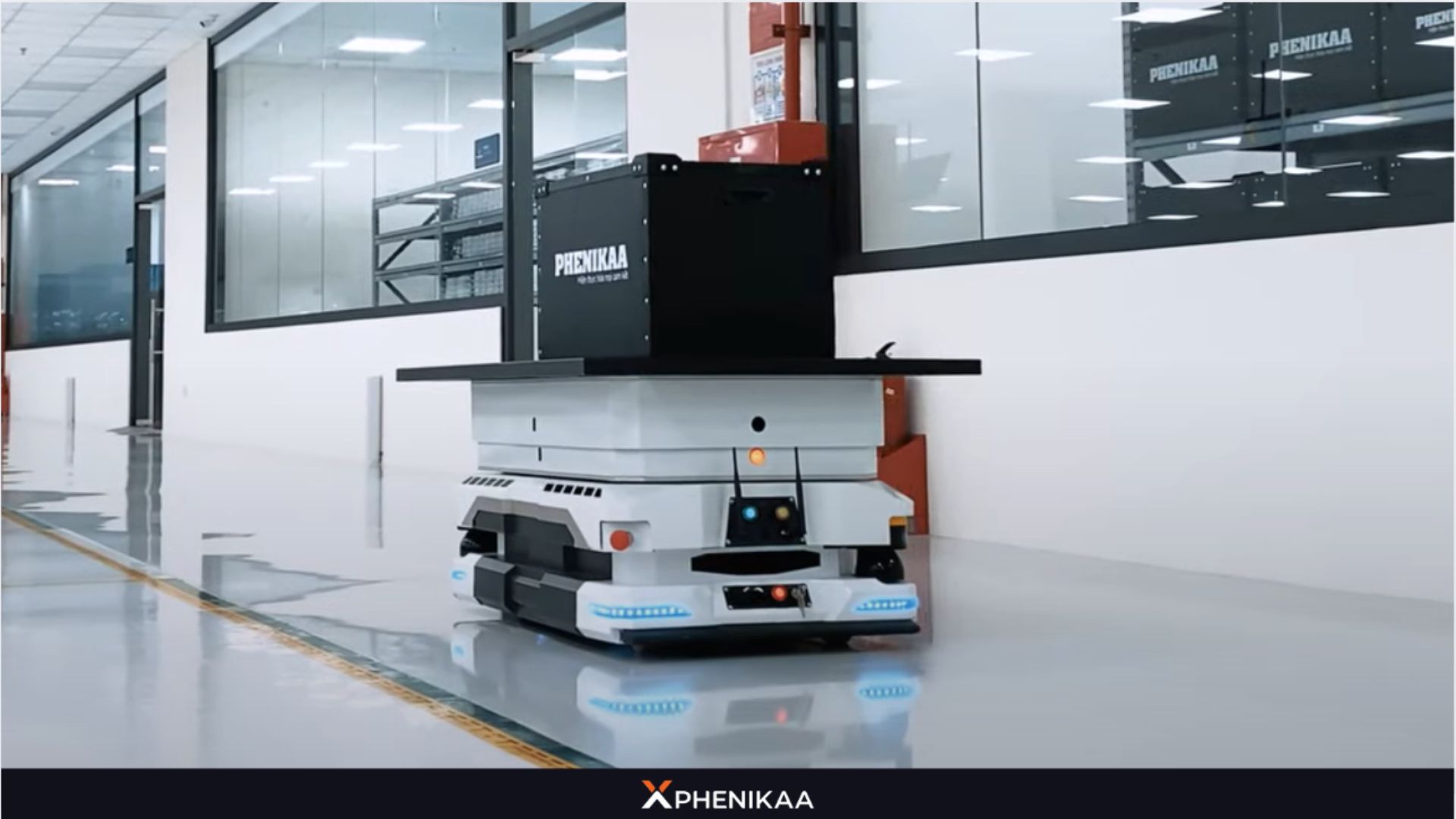
The versatility of AGVs in manufacturing shines through in their wide-ranging applications. Here’s how they’re used:
- Material Handling: AGVs in manufacturing excel at moving raw materials, components, and finished products. They eliminate the need for manual forklifts, speeding up workflows and reducing errors.
- Assembly Line Support: In industries like automotive or electronics, manufacturing AGV deliver parts to workers exactly when needed, supporting just-in-time production. Companies like Toyota have long relied on this approach.
- Warehouse Automation: Within factories, AGVs in manufacturing manage inventory, shuttling goods between storage and production zones with pinpoint accuracy.
- Heavy Load Transport: For industries like steel or aerospace, manufacturing AGV handle massive loads that would be risky or impractical for humans to move. Let’s take Tesla, for instance, uses AGVs in manufacturing to streamline its electric vehicle production, while Vietnamese firms, as noted by Phenikaa-X company, adopt them for industrial efficiency.
3. Benefits of Using AGV in Manufacturing
Why are AGVs in manufacturing so popular in recent years? It is due to benefits they bring to the industrial are hard to ignore:
- Efficiency: They cut downtime and accelerate material transport, boosting throughput by up to 25%, according to AutoStore.
- Cost Savings: Fewer workers are needed for repetitive tasks, and errors drop significantly.
- Safety: Manufacturing AGVs take over dangerous jobs, like moving heavy loads in tight spaces.
- Scalability: Need more capacity? Add another AGV to the fleet.
- Sustainability: Modern AGVs in manufacturing use energy-efficient designs, shrinking a factory’s carbon footprint.
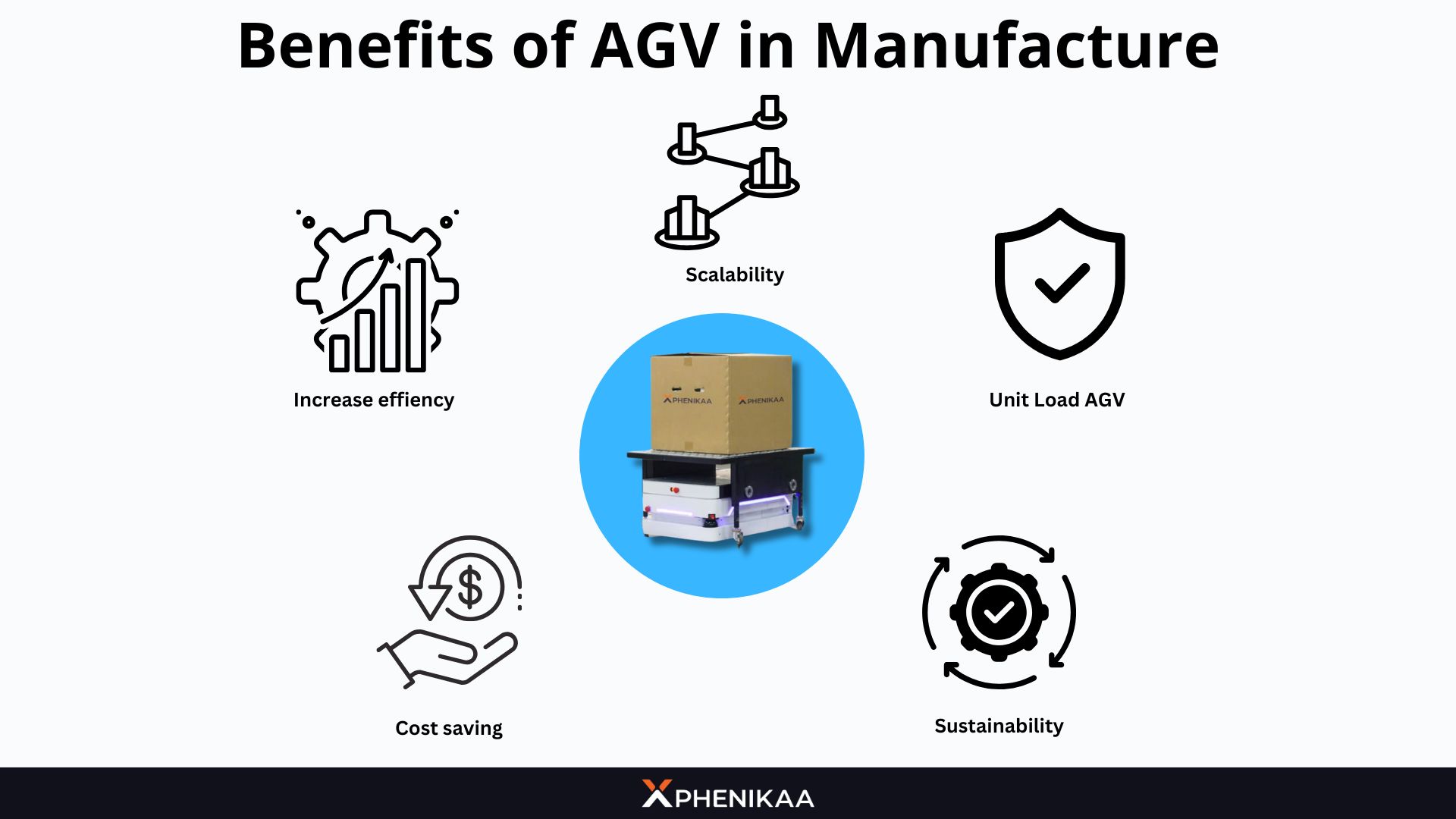
These advantages make AGVs in manufacturing a smart investment for companies aiming to stay competitive.
4. Current Challenges and Limitations of AGVs in Manufacturing
Despite their strengths, AGVs in manufacturing aren’t without drawbacks. The initial cost of buying and integrating them can be steep, often running into hundreds of thousands of dollars. Maintenance is another hurdle-sensors and batteries need regular care, and software updates can be complex. Flexibility is limited too; if a factory layout changes, reprogramming an AGV in manufacturing takes time and expertise.
The other issue is operating these systems requires trained staff, which can be a barrier for smaller businesses. Still, with proper planning, these challenges can be managed to unlock the full potential of manufacturing AGV.
5. Assessment of AGV Applications in Manufacturing in Vietnam and Southeast Asia
The adoption of AGVs in manufacturing has gained significant traction globally, and Southeast Asia (SEA), including Vietnam, is no exception. As the region positions itself as a manufacturing hub, driven by low labor costs and growing industrial output, AGV in manufacturing are increasingly seen as a tool to enhance efficiency, reduce costs and align with Industry 4.0 trends.
However, the pace and scale of adoption in Vietnam and SEA differ from more developed markets due to economic, technological, and infrastructural factors.
Current State in Vietnam
In Vietnam, the use of AGVs in manufacturing is still in its early stages but shows promising growth. The country’s manufacturing sector, particularly in electronics, textiles, and automotive industries, has been a key driver of economic development. Big companies like Samsung, LG are investing in automation to stay competitive.
Manufacturing AGVs are primarily deployed in large-scale factories in industrial zones like Hanoi, Ho Chi Minh City, and Bac Ninh, where they handle material transport, assembly line support, and warehouse logistics.

Trends in Southeast Asia
Across SEA, the application of AGV in manufacturing varies by country but is accelerating due to regional economic integration and demand for high-quality production. Here are some information on the topic:
- Singapore and Malaysia: The 2 countries are one of the earliest using AGV on industrial, leveraging their advanced infrastructure and tech-savvy workforce. In Singapore, manufacturing AGV are integral to smart factories, supporting industries like semiconductors and pharmaceuticals with precision and scalability. Malaysia’s automotive sector uses AGVs in manufacturing to streamline assembly lines and logistics.
- Thailand: The country known for its automotive manufacturing, is also adopting AGV in manufacturing to meet export demands, with companies integrating them into just-in-time production systems. Indonesia, while lagging slightly, is seeing growth in manufacturing AGVs in food processing and consumer goods sectors, driven by urbanization and E-commerce.
6. The Role of AGV in Industry 4.0
In the era of smart factories, AGV in manufacturing are more than just movers—they’re data hubs. Integrated with the Internet of Things (IoT) and Artificial Intelligence (AI), they track goods in real time and optimize routes on the fly. This aligns perfectly with Industry 4.0’s focus on connectivity and automation.
For instance, a manufacturing AGV might alert operators to a production bottleneck before it escalates. Looking ahead, experts predict AGV in manufacturing will evolve into swarm-like systems, coordinating like a hive to maximize efficiency.
Let’s compare AGVs in manufacturing with traditional methods. Here are several key differences:
- Manual Labor: Humans are slower and prone to fatigue, while manufacturing AGVs work tirelessly with consistent precision.
- Conveyor Systems: Conveyors are fixed and costly to reconfigure; AGVs in manufacturing offer flexibility and lower long-term costs.
Aspect | Manual Labor | Conveyors | AGV |
Speed | Slow | Moderate | High |
Flexibility | High | Low | High |
Initial Cost | Low | High | High |
Safety | Risky | Moderate | High |
Clearly, AGV in manufacturing shine in modern, dynamic settings. The technology allows industry to move their work force into other more important and safetier tasks, while leaving the danger and repetitive jobs for the Robot.
7. Future Trends in AGVs for Manufacturing
Across the globe, AGV in manufacturing are making waves with big names start to notice their potential. For example:
- BMW uses them to shuttle parts in its German plants, cutting production time significantly.
- Amazon’s warehouses rely on manufacturing AGVs to handle millions of packages daily.
- In Vietnam, as TPA-FAS reports, local factories are adopting AGVs in manufacturing to boost competitiveness in industries like electronics and textiles.
These success stories show how AGV in manufacturing deliver measurable gains—some firms report productivity jumps of 20-30%. Not to stop at that, the advance of AI-tech will make them smarter, enabling self-learning capabilities to adapt to new tasks. Collaborative manufacturing AGVs will work side-by-side with humans, enhancing teamwork on the factory floor.
8. How to Implement AGVs in Your Manufacturing Facility?
Ready to bring AGVs in manufacturing to your plant? Follow these steps:
- Assess Needs: Map your factory’s layout and material flow to identify AGV opportunities.
- Choose the Right Type: Pick a manufacturing AGV suited to your loads and tasks.
- Plan Integration: Sync AGVs with existing systems like MES or ERP.
- Train Staff: Ensure your team can operate and maintain the fleet.
Most importantly, having a proper AGV manufacturer is the key to making your smart factory a reality. Partnering with a reliable provider ensures your AGVs in manufacturing are tailored to your needs, built for durability, and supported with expert guidance. A trusted manufacturer can make the difference between a good investment and a great one.
Start small with a pilot project, then scale up as you measure the benefits. Monitoring ROI will help you see the full impact of manufacturing AGV on your bottom line. Ready to take the next step? Explore cutting-edge AGV solutions with Phenikaa-X, a leader in smart manufacturing technology, and transform your facility today.
Conclusion
From boosting efficiency to enhancing safety, AGVs in manufacturing are revolutionizing how we build products. These autonomous wonders cut costs, streamline workflows, and pave the way for smarter factories. Whether you’re in automotive, electronics, or heavy industry, a manufacturing AGV could be the key to staying ahead.
Phenikaa-X is one of the best AGV and robotic solutions providers in the Asia and we are now shipping worldwide. Contact us today to learn more about integrating AGVs into your business:
- Facebook: https://www.facebook.com/phenikaa.x
- Hotline: (+84) 904530545
- Email: contact@phenikaa-x.com