Automated Guided Vehicles (AGV) and Autonomous Mobile Robots (AMR) are two pivotal technologies driving efficiency in manufacturing industries. But what to choose between AGV and AMR? Which is more suitable for your factory? Join Phenikaa X on comprehensive guide dives deep into the AGV vs AMR comparison, highlighting their similarities, key differences and some example of their real-world uses to help businesses make informed decisions.
1. What Are AGVs and AMRs?
Before delving into the key differences in the AGV vs AMR debate, you first need to understand what these technologies are. Both Robot technologies are two cornerstone innovations in industrial automation, designed to streamline material handling and enhance operational efficiency.
While they share the common goal of reducing manual labor and optimizing workflows, their approaches and capabilities set them apart. Let’s break down their definitions to lay the groundwork for a deeper comparison.
1.1. What is Automated Guided Vehicle (AGV)
Automated Guided Vehicles (AGV) are self-driving vehicles designed to follow predetermined paths, typically guided by physical markers like magnetic strips, wires, or laser targets embedded in the floor. Introduced decades ago, AGVs have been a staple in industrial automation, excelling in repetitive tasks such as transporting goods between fixed points in warehouses or moving materials along production lines. Their reliance on fixed infrastructure, however, limits their adaptability.
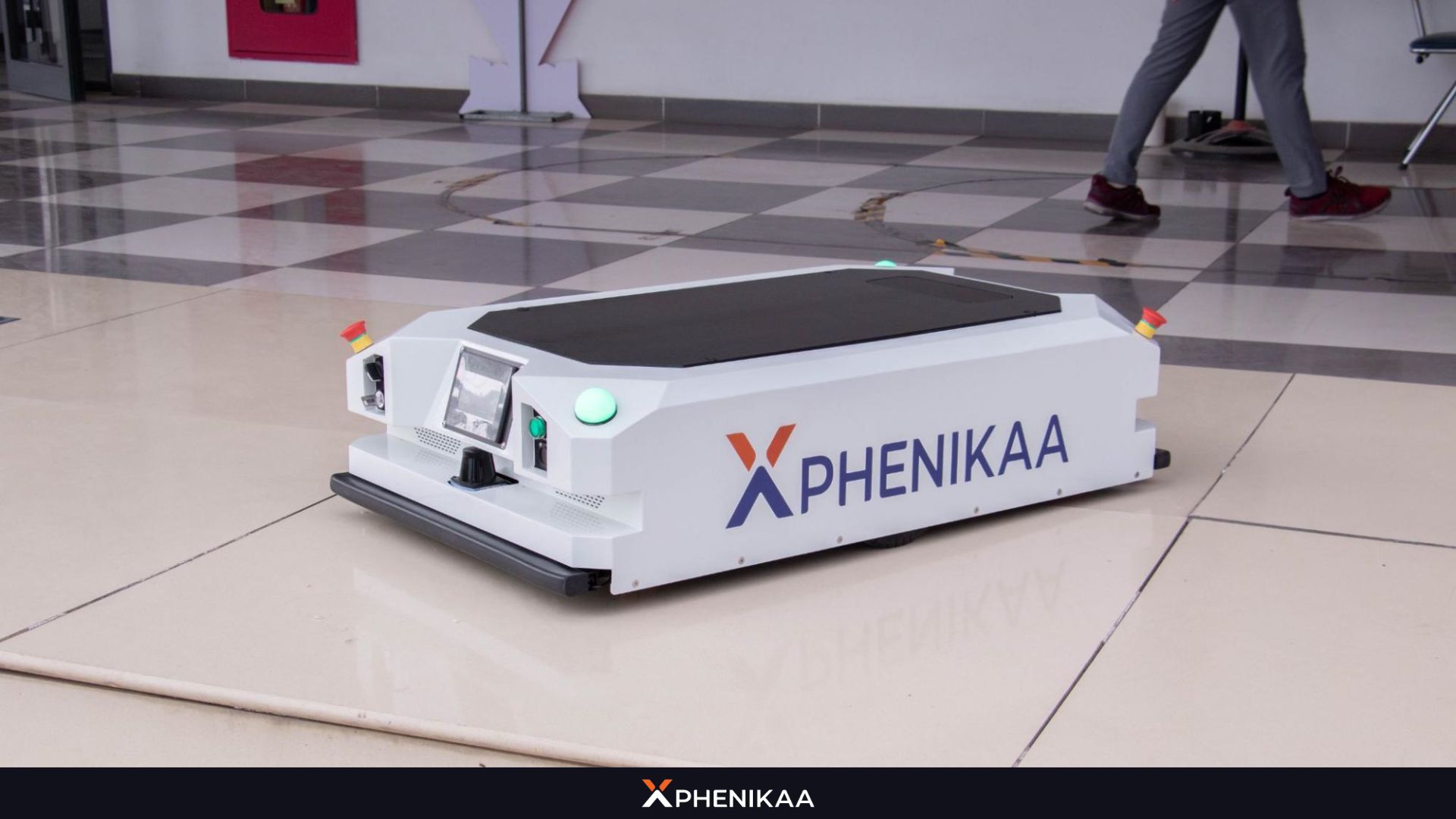
The concept of AGV robots is to eliminate the need for human oversight by integrating robotics, software, and sensors to optimize industrial processes. They excel at tasks such as picking up heavy loads from one location, transporting them across a facility, and delivering them to a designated spot – all while avoiding obstacles and coordinating with other equipment. Some AGVs can even collaborate with human workers or other machines, showcasing their adaptability in dynamic settings.
1.2. Autonomous Mobile Robot (AMR)
Autonomous Mobile Robots (AMR) are advanced robotic systems designed to move and operate independently in dynamic environments without requiring human intervention or predefined paths. Unlike traditional robots that depend on fixed routes, AMR robots are equipped with sophisticated sensors, artificial intelligence (AI), and machine learning capabilities. These technologies enable them to navigate complex spaces, avoid obstacles, and perform tasks with remarkable efficiency.
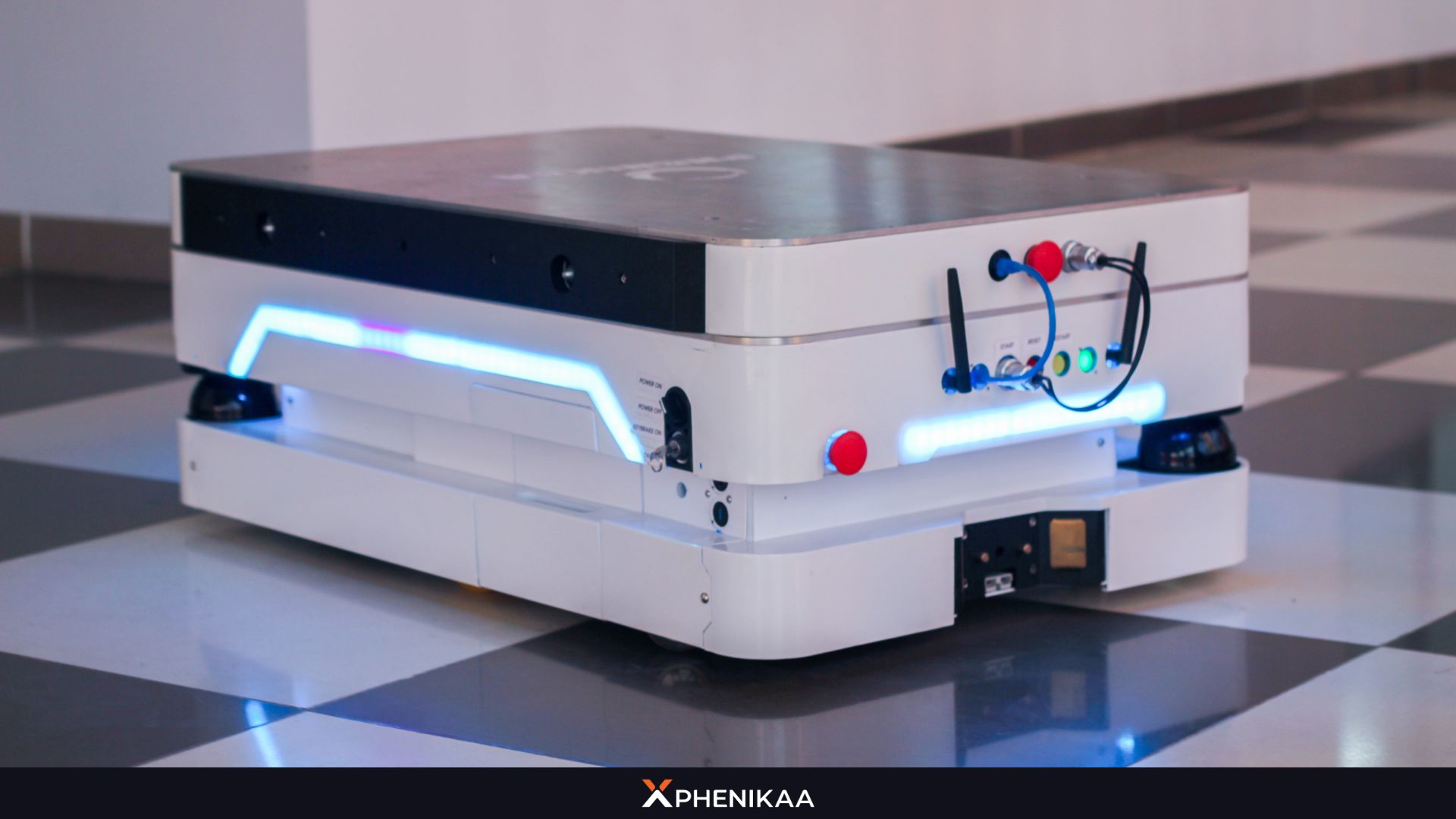
AMR robot is one of the recent attempts to create intelligent machines capable of autonomously handling repetitive, labor-intensive tasks to enhance operational efficiency and reduce reliance on human labor. These robots can operate in real-time, navigate without predefined paths, and even learn from their surroundings to optimize performance – a significant departure from traditional automation’s reliance on rigid patterns.
In the AGV vs AMR debate, understanding these foundational differences is key to choosing the right solution for your operational needs.
2. The Similarities Between AMR and AGV
Since both are automobile robots, it is fair to understand why usually people have trouble distinguishing them. AGVs and AMRs have in common:
- Automation Focus: Both AGVs and AMRs aim to automate material handling, reducing human effort and minimizing non-value-added travel in warehouses and factories.
- Safety Features: Each robot are equipped with sensors and different safety systems, to ensure safety for humans and facilities by detecting obstacles and preventing collisions.
- Efficiency Gains: Whether it’s moving pallets or delivering components, AGVs and AMRs enhance productivity by streamlining workflows.
- Industrial Applications: Both are widely used in manufacturing, warehousing, and logistics to optimize operations.
From those, it is understandable how people often mistake AMR and AGV functionalities and purpose to each other. While these similarities make them valuable automation tools, the AMR vs AGV distinction lies in their flexibility, navigation, and adaptability.
3. AGV vs AMR: Key Differences
There are lots of differences between these two technologies. Here are the short comparison:
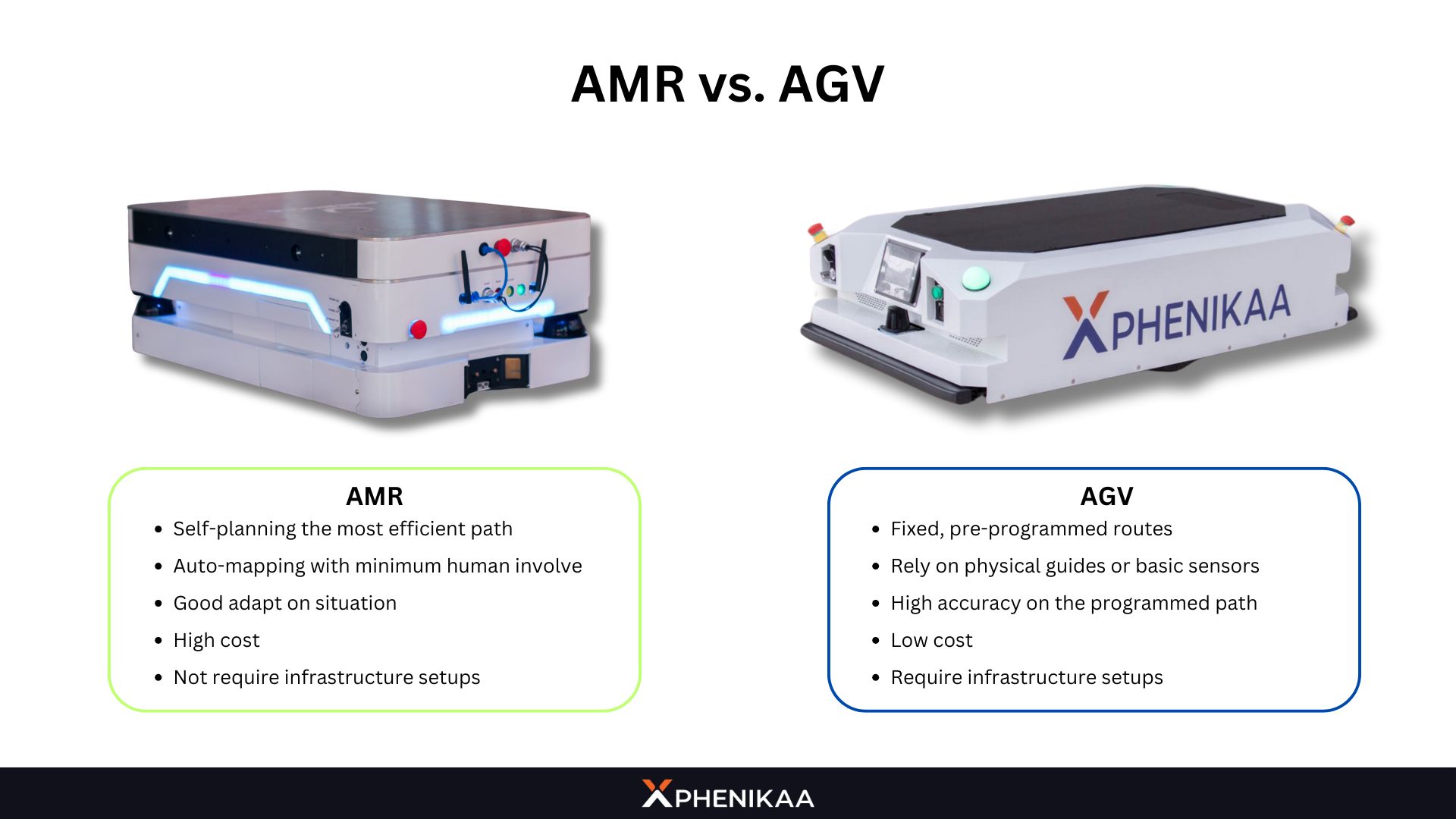
3.1. Navigation and Path Planning
AGVs operate on fixed, pre-programmed routes. They rely on physical guides or basic sensors to follow a “virtual line”. This rigidity means AGVs cannot deviate from their paths or adapt to changes without manual reconfiguration. If an obstacle blocks their route, AGVs stop and require human intervention to resume.

While AMRs, on the other hand, use sophisticated navigation technologies like Simultaneous Localization and Mapping (SLAM) and 3D sensor fusion. They assess multiple routes, dynamically planning the most efficient path to their destination. In the AGV vs AMR comparison, AMRs stand out for their ability to reroute around obstacles autonomously, ensuring uninterrupted operation.
3.2. Obstacle Avoidance
AGVs have limited obstacle avoidance capabilities. When encountering a blockage, they halt until the path is cleared, often necessitating a physical reset. This makes them less suited for crowded or unpredictable environments.
AMRs excel in obstacle avoidance. Their advanced sensors detect people, objects, or blockages in real-time, allowing them to adjust their paths or find alternate routes. This adaptability is a critical differentiator in the AGV vs AMR discussion.
3.3. Flexibility and Scalability
AGVs are best for structured environments with consistent workflows. Changing their routes or expanding their use requires reinstalling guides or reprogramming, which can be time-consuming and costly.
AMRs offer unmatched flexibility. They can be deployed quickly—sometimes in under 15 minutes—and adapt to evolving needs without infrastructure changes. In the AGV vs AMR showdown, AMRs’ scalability makes them a future-proof choice for growing businesses.
3.4. Payload Handling
AGVs dock to payloads at predetermined locations, requiring precise alignment. Misaligned pallets or goods often demand human intervention, slowing operations.
AMRs dynamically adjust to misaligned payloads, using sensors to locate and pick items accurately. This capability enhances efficiency in the AGV vs AMR comparison.
3.5. Cost Considerations
AGVs typically have a lower upfront cost per unit. However, their installation involves significant expenses—think underfloor wiring or magnetic tape—plus ongoing maintenance and reconfiguration costs. In dynamic settings, these hidden costs can outweigh initial savings.
In contrast, AMRs may carry a higher per-unit price, but their lack of infrastructure requirements and rapid deployment offset this. Business owners can simply buy the AMR, make some standard setups (system and software, with minimum placements) and the AMR is ready to go, without any further cost. This makes a huge consideration of when to pick in the AGV vs AMR analysis.
AGV vs AMR Side-by-Side Comparison Table:
Feature | AGV | AMR |
Navigation | Fixed routes (magnetic tape, wires) | Dynamic (LiDAR, SLAM, cameras) |
Obstacle Avoidance | Stops until path is clear | Reroutes around obstacles |
Flexibility | Limited; requires reconfiguration | High; adapts in real-time |
Payload Handling | Requires precise alignment | Adjusts to misaligned payloads |
Cost | Lower unit cost, high setup cost | Higher unit cost, low setup cost |
Best For | Repetitive, structured tasks | Dynamic, variable workflows |
This table encapsulates the core distinctions in the AGV vs AMR debate, guiding businesses toward the best fit for their needs.
4. Applications of AGVs and AMRs in Real Life
Both AGVs and AMRs have transformative applications across industries. Let’s explore how they’re deployed in real-world scenarios.
Applications of AGVs
- Manufacturing: AGVs shine in assembly lines, transporting raw materials or finished goods between fixed stations. For example, in automotive plants, AGVs move heavy components like engines or chassis with precision.
- Warehousing: AGVs handle repetitive tasks like moving pallets from storage to shipping areas, thriving in environments with predictable layouts.
- Pharmaceuticals: In controlled settings, AGVs transport sensitive materials, ensuring consistency and minimizing human contact.
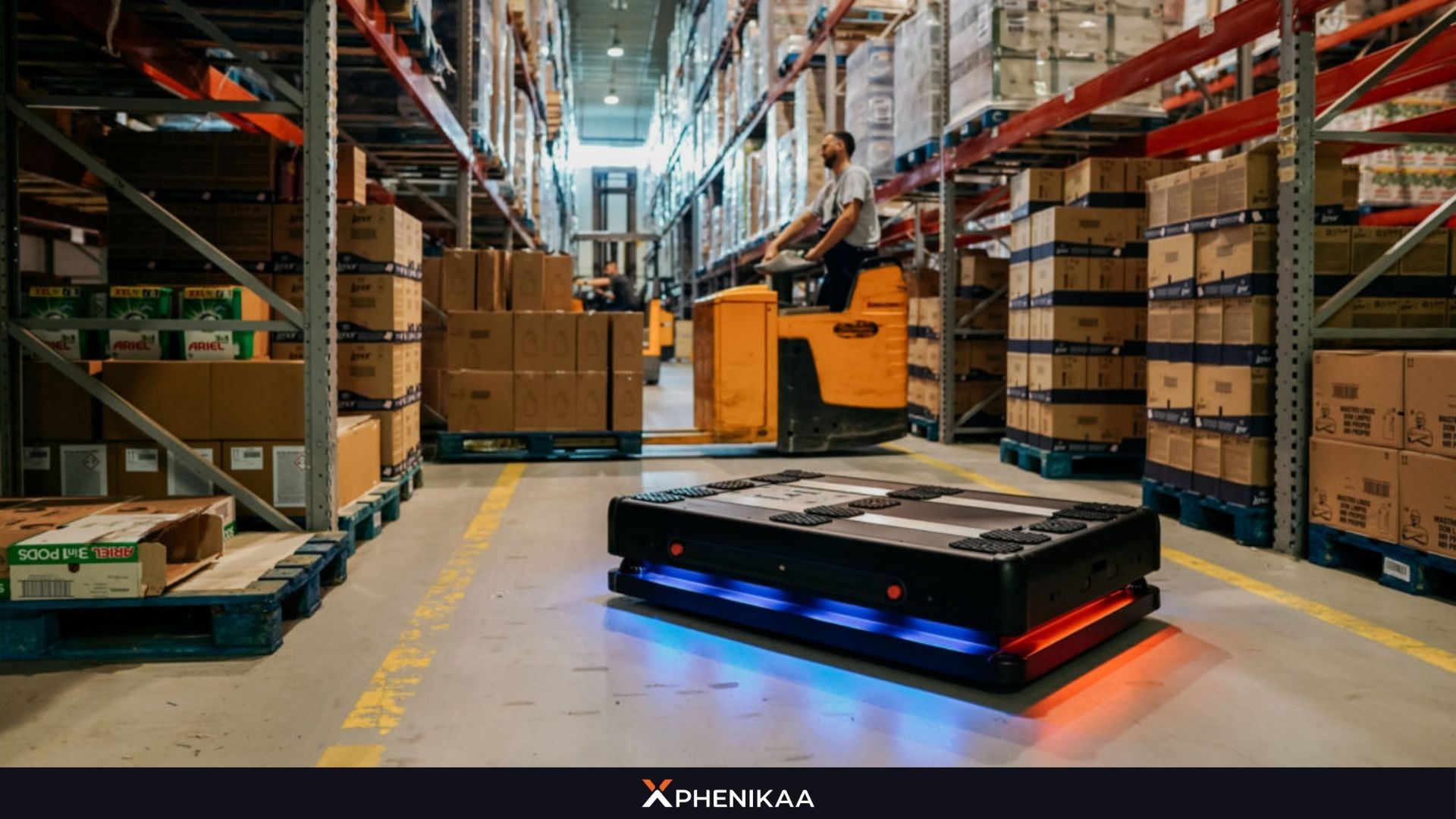
In the AGV vs AMR context, AGVs are ideal for stable, unchanging workflows where precision trumps adaptability.
Applications of AMRs
- E-commerce Warehousing: AMRs excel in large, dynamic warehouses, navigating narrow aisles and crowded spaces to pick and sort orders. Companies like Amazon use AMRs to meet fluctuating demand.
- Just-In-Time (JIT) Manufacturing: AMRs deliver materials to production lines as needed, adapting to real-time changes in demand or layout.
- Healthcare: In hospitals, AMRs transport supplies, medications, or linens, navigating busy corridors without disrupting staff or patients.
The AGV vs AMR comparison highlights AMRs’ edge in environments requiring agility and responsiveness.
Hybrid Use Cases
In some cases, businesses combine AGV and AMR for hybrid automation. For instance, AGVs might handle long-haul transport along fixed routes, while AMRs manage flexible, short-range tasks like order picking. This synergy maximizes efficiency in complex operations.
5. AGV vs AMR: Which Should You Choose?
Choosing between AGVs and AMRs depends on your operational goals, budget, and environment. Here’s a breakdown to guide your decision:
When to Choose AGVs
- Stable Workflows: If your facility has consistent processes and layouts that rarely change, AGVs offer a reliable, cost-effective solution.
- Repetitive Tasks: For high-volume, repetitive material handling—like moving goods between two fixed points—AGVs deliver precision and predictability.
- Budget Constraints: If upfront cost is a priority and you can afford the infrastructure investment, AGVs might suit your needs.
Although AGV Robot standalone has lower cost than AMR, the expenses involved in setting up, deploying, reconfiguring and operating them also need to be considered. AGVs often require the installation of physical guides, underfloor wiring, or surface tape to enable navigation and positioning within their surroundings, which might end up in whole facility renovation in some cases.
When to Choose AMR
- Dynamic Environments: In fast-paced settings with frequent changes-think e-commerce or agile manufacturingAMRs’ adaptability is unmatched.
- Scalability Needs: If you anticipate growth or workflow shifts, AMRs’ easy deployment and flexibility make them a future-ready choice.
- Cost and Implementation Time: For businesses prioritizing quick implementation or lacking the budget for extensive facility upgrades, AMRs are a smarter investment.
In contrast, a great AMR requires no modifications to your existing facility and can autonomously navigate through production spaces and warehouses. It learns its environment, remembers its location, and automatically plans its path from one destination to another. If its route is blocked, the AMR can reroute itself without assistance. Of course, these features come with more expensive costs for each individual AMR unit than AGV.
6. The Future of AGV vs AMR in Automation
As automation evolves, the AGV vs AMR rivalry will shape the future of robotics. AGVs will likely remain relevant in niche, highly structured applications, but AMRs are poised to dominate thanks to their intelligence and versatility. Innovations like continuous learning and Robotics-as-a-Service (RaaS) pricing models further tilt the scales toward AMRs.
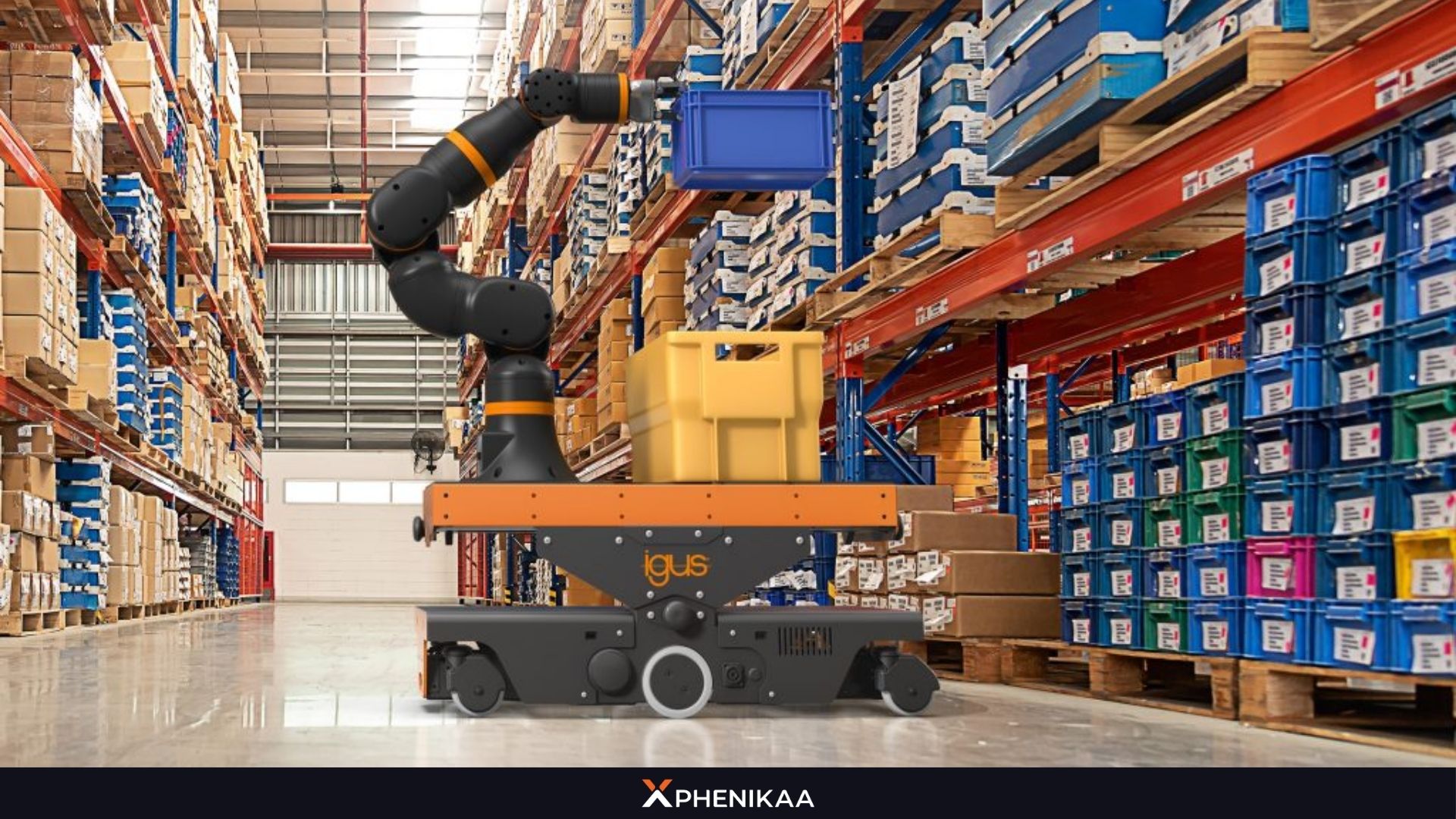
In the AGV vs AMR narrative, AMRs align with the demands of modern industries-flexibility, scalability, and responsiveness – while AGVs cater to traditional, predictable workflows. Businesses must weigh these factors against their unique needs to stay competitive.
Conclusion
The AGV vs AMR comparison reveals two powerful yet distinct tools in the automation toolkit. AGVs offer reliability for repetitive, structured tasks, while AMRs bring agility and intelligence to dynamic environments. From manufacturing lines to bustling warehouses, their applications demonstrate their value in enhancing efficiency and reducing costs.
Phenikaa X is a Vietnam-based manufacturer specializing in providing autonomous technology solutions to partners across Asia and worldwide. We offer advanced robotic systems such as AGVs, AMRs, Drone-in-a-box, Autonomous Vehicles, Service Bots, and more, catering to manufacturers, service businesses and healthcare providers. Our goal is to deliver the most professional and efficient services possible.
If you are interested in learning more about AGV and AMR products, please contact us at:
- Facebook: https://www.facebook.com/phenikaa.x
- Hotline: (+84) 904530545
- Email: contact@phenikaa-x.com